January 15, 2025
By Jennifer McKeogh, senior manager, GM communications
Teams across General Motors are always innovating to create more efficient processes, cost-effective designs and safer practices. Additive manufacturing is one way we’re innovating across our footprint — from pre-production to motorsports.
Often referred to as 3D printing, additive manufacturing is a process that creates complex three-dimensional parts directly from digital designs by building up layers of material one at a time. GM has been using additive manufacturing for more than 30 years in applications across design, product and materials engineering, vehicle manufacturing, and aftersales to make components ranging from body hardware to electrical, interiors and more.
Here are a few ways GM currently uses additive manufacturing:
- Early part prototypes to supplement virtual designs
- Simplification of tools and fixtures
- Operator assists in manufacturing plants
- Cost-effective and durable production components
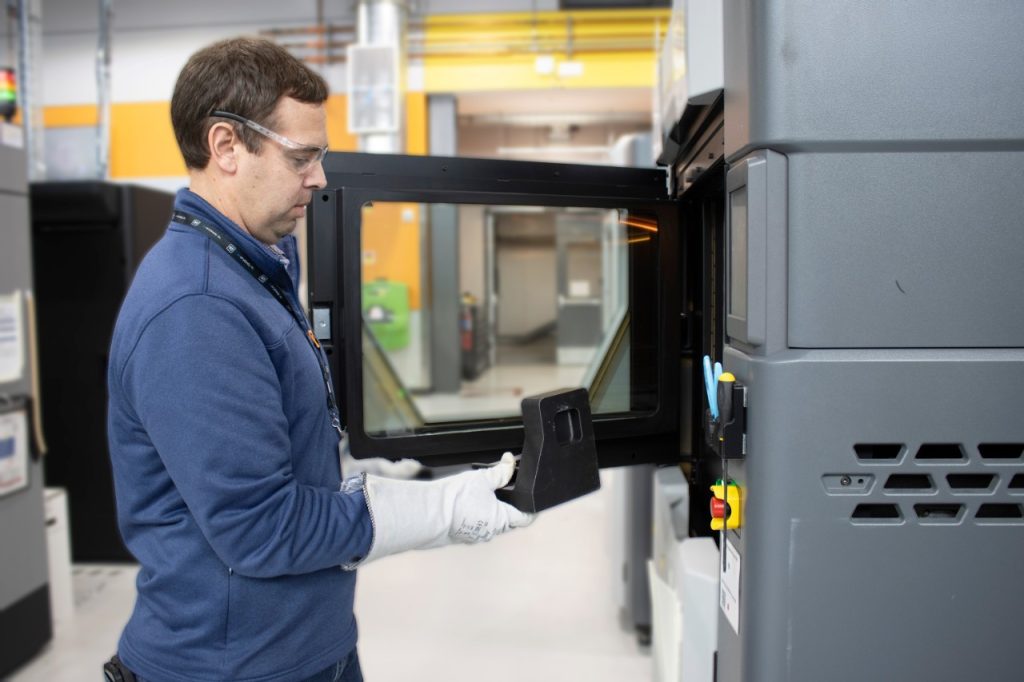
One use for additive manufacturing is improving our in-plant processes, including ergonomic solutions for employees who work on the line.
For example, team members at Lansing Delta Township Assembly — home to the Buick Enclave, Chevrolet Traverse, and GMC Acadia — found a way to use additive manufacturing that makes vehicle assembly even easier.
Assembly line operators previously used a metal fixture to prop open vehicle hoods before attaching them to their hinges. These titanium and steel fixtures weigh in at 14 pounds — heavier than the 10-pound limit for a one-hand lift. After exploring other options to lighten the part, the plant engaged our additive manufacturing team to develop a new, lighter design.
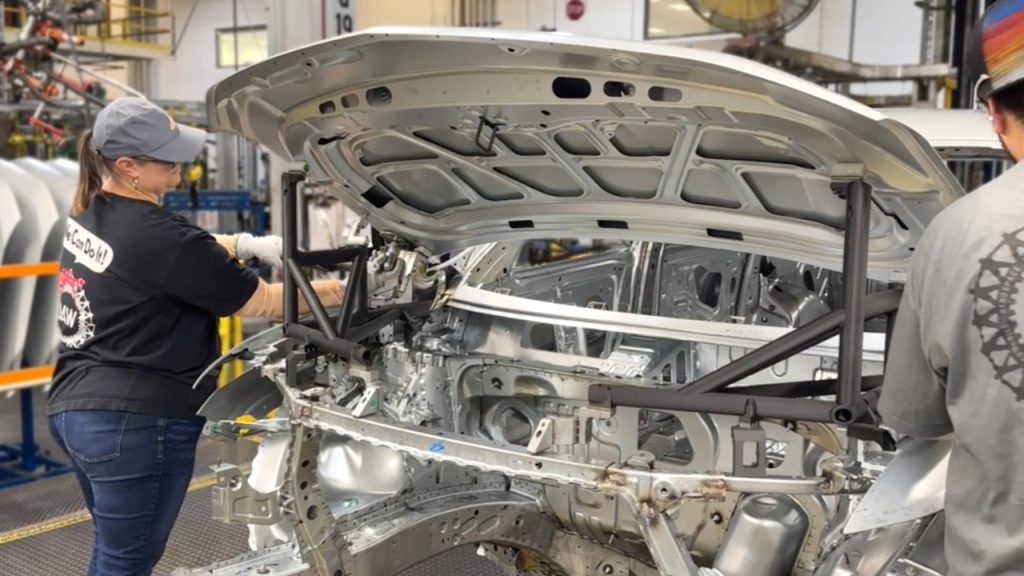
“Additive manufacturing continues to enable us to build our vehicles safer and quicker,” said Paul Wolcott, a GM technical specialist. “From accelerated lead times for tools to addressing ergonomic issues with lightweight solutions, we keep seeing growth in applications the more we implement it.”
In 2024 alone, GM executed over 5,400 new additive manufacturing projects — and the applications keep coming, with even more expected in 2025.
As we move toward an all-electric future, innovations like additive manufacturing will help enable GM to bridge the virtual gap and solve problems — from ergonomics, design, in-house manufacturing solutions, and more.