By Kurt Kelty, VP, battery, propulsion, and sustainability, General Motors
When I joined the battery industry 30 years ago, the focus was on consumer electronics, like powering handheld camcorders. Today, General Motors is delivering full-size electric trucks with up to 492 miles of range. The progress in lithium-ion battery technology has been remarkable – but the real transformation is just beginning.
At GM, we’re not just building better batteries. We’re scaling U.S. production, securing a resilient North American supply chain, and advancing technology to drive down costs and compete globally. I shared our vision for the future of U.S. battery industrialization earlier this month at the SAFE Summit, a policy forum in Washington, D.C. Here’s what I discussed:
Scaling manufacturing
Competing in the global battery technology race requires the ability to produce at scale, and we are doing just that. Ultium Cells, our joint venture with LG Energy Solution, is the largest OEM battery cell producer in North America, with quality and yield that rival the best in the world.
Our technology investments have helped GM become the #2 seller of electric vehicles in the U.S., with first-quarter EV sales up 94%. We offer the industry’s most diverse EV portfolio, with a dozen models in the market.
Our new joint venture with Samsung SDI, launching in Indiana in 2027, will allow us to produce prismatic cells, an additional form factor that gives us the flexibility to deliver the right battery technology to further optimize foreach vehicle and customer need.
Localizing the supply chain
Batteries are the heart of EVs, and the materials that go into them matter. That’s why we’re going beyond cell production in the U.S., and securing North American sources for lithium, manganese, and nickel, and investing in localizing production of cathodes, anodes, electrolytes, and separators. By 2028, we’ll increase North American content in our battery supply chain eightfold.
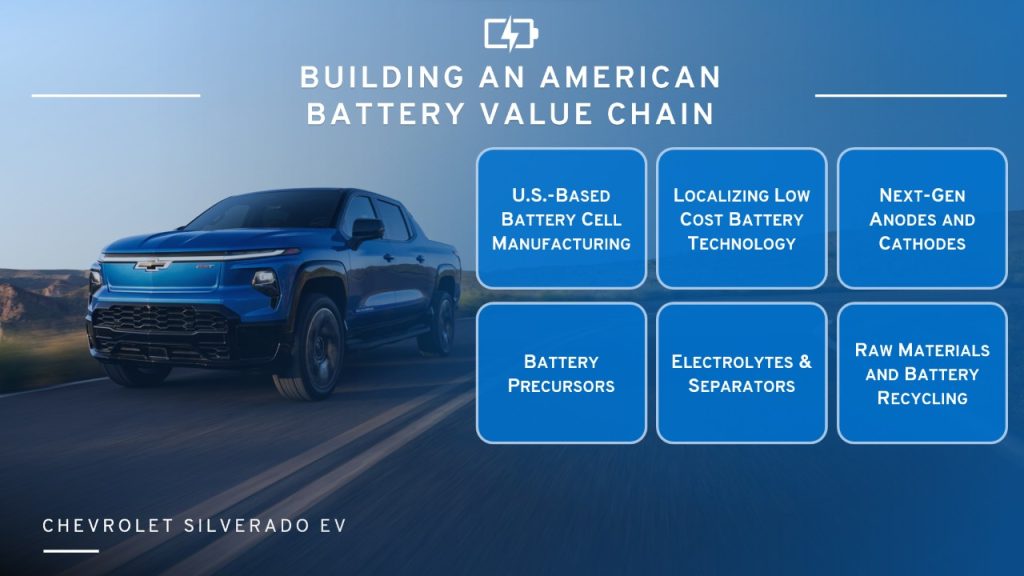
American innovation
At GM, we’re engineering the right battery for the right vehicle, optimizing for performance, cost, and range across our portfolio. That includes expanding our platform to use prismatic cells, which reduces battery module components by 75% and total pack components by 50%. Combined with low-cost LFP (lithium iron phosphate) chemistry, this innovation will cut $6,000 per pack in a Chevrolet Silverado EV, helping us deliver more range and value to more customers.
Our battery innovation is driven by our in-house R&D team. At the Wallace Battery Cell Innovation Center, on our campus in Warren, Michigan, we’re developing advanced new, next-generation battery cell chemistries that bridge the gap between energy density and cost. And with our Battery Cell Development Center being constructed next door in Warren, we’ll accelerate the path from lab to gigascale production, driving vehicle innovation and consumer choice.
The road ahead
GM spends about $7 billion in the U.S. on research and development each year, advancing American jobs, technological progress, and manufacturing excellence. The U.S. has the talent, technology, and investment to lead in electrification. We also have the local demand. By scaling battery innovation, localizing production and supply chain, and delivering more affordable EVs, GM is positioning itself and the U.S. to compete—and win—on the global stage.
Kurt Kelty has been working in the battery sector for more than 30 years. Now VP of battery, propulsion and sustainability, he joined General Motors in February 2024. Contact: news@gm.com
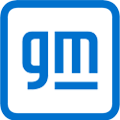
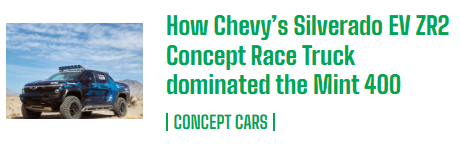